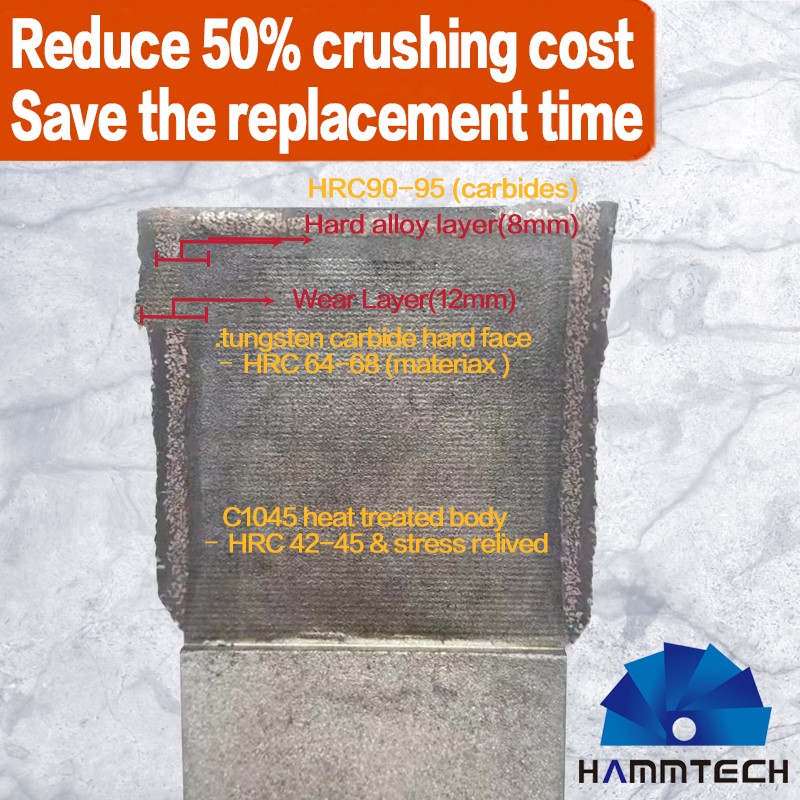
1. A trituradora experimenta vibracións fortes e anormais
Motivo: A causa máis común de vibración débese ao desequilibrio da plataforma xiratoria, que pode ser causado por unha instalación e disposición incorrectas das láminas do martelo; as láminas do martelo están moi desgastadas e non foron substituídas a tempo; algunhas pezas do martelo están atascadas e non se soltan; os danos noutras partes do rotor provocan un desequilibrio de peso. Outros problemas que causan vibracións inclúen: deformación do eixo debido á folgura; o desgaste severo dos rolamentos pode causar danos; parafusos de cimentación soltos; a velocidade do martelo é demasiado alta.
Solución: Volver instalar as láminas do martelo na orde correcta; Substituír a lámina do martelo para garantir que a desviación do peso da lámina do martelo non supere os 5 g; Apagar a inspección, manipular o martelo para facer que a peza atascada xire normalmente; Substituír as pezas danadas do prato xiratorio e equilibrala; Endereitar ou substituír o eixo; Substituír os rolamentos; Fixar firmemente os parafusos de cimentación; Reducir a velocidade de rotación.
2. A trituradora fai ruído anormal durante o funcionamento
Motivo: Obxectos duros como metais e pedras entran na cámara de trituración; Pezas soltas ou separadas dentro da máquina; O martelo rompeu e caeu; O espazo entre o martelo e o coador é demasiado pequeno.
Solución: Pare a máquina para inspeccionala. Axuste ou substitúa as pezas; Retire os obxectos duros da cámara de trituración; Substitúa a peza rota do martelo; Axuste a separación entre o martelo e o cribo. A separación óptima para grans xerais é de 4-8 mm e para palla, de 10-14 mm.
3. O rolamento está sobrequentado e a temperatura da carcasa da máquina de trituración é moi alta
Motivo: Danos nos rolamentos ou aceite lubricante insuficiente; Correa demasiado tensa; Alimentación excesiva e traballo de sobrecarga a longo prazo.
Solución: Substituír o rolamento; Engadir aceite lubricante; Axustar a tensión da correa (premer o centro da correa de transmisión coa man para crear unha altura de arco de 18-25 mm); Reducir a cantidade de alimentación.
4. Aire invertido na entrada de alimentación
Motivo: Bloqueo do ventilador e da tubaxe de transporte; Bloqueo dos orificios do peneiro; A bolsa de po está demasiado chea ou demasiado pequena.
Solución: Comprobe se o ventilador está excesivamente desgastado; Limpe os buratos do coador; Descargue ou substitúa a bolsa de recollida de po a tempo.
5. A velocidade de descarga diminuíu significativamente
Motivo: A lámina do martelo está moi desgastada; A sobrecarga da trituradora fai que a correa escorregue e provoque unha baixa velocidade do rotor; Obstrución dos orificios da peneira; O espazo entre o martelo e a peneira é demasiado grande; Alimentación desigual; Potencia de soporte insuficiente.
Solución: Substitúa a folla do martelo ou cámbieaa; Reduza a carga e axuste a tensión da correa; Limpe os buratos da peneira; Reduza a separación entre o martelo e a peneira de forma axeitada; Alimentación uniforme; Substitúa o motor de alta potencia.
6. O produto acabado é demasiado groso
Motivo: Os orificios da peneira están moi desgastados ou danados; Os orificios da malla non están firmemente unidos ao soporte da peneira.
Solución: Substitúa a malla da criba; axuste o espazo entre os orificios da criba e o soporte da criba para garantir un axuste perfecto.
7. Sobrequecemento da correa
Motivo: Apertura incorrecta da correa.
Solución: Axuste a tensión da correa.
8. A vida útil da folla do martelo redúcese
Motivo: Un contido excesivo de humidade no material aumenta a súa resistencia e tenacidade, o que o fai máis difícil de esmagar; Os materiais non están limpos e mesturados con obxectos duros; O espazo entre o martelo e o coador é demasiado pequeno; A calidade da folla do martelo é demasiado deficiente.
Solución: Controlar o contido de humidade do material a non máis do 5 %; Minimizar o contido de impurezas nos materiais tanto como sexa posible; Axustar a separación entre o martelo e o coador de forma axeitada; Empregar pezas de martelo resistentes ao desgaste de alta calidade, como as tres pezas de martelo de alta aliaxe de Nai.
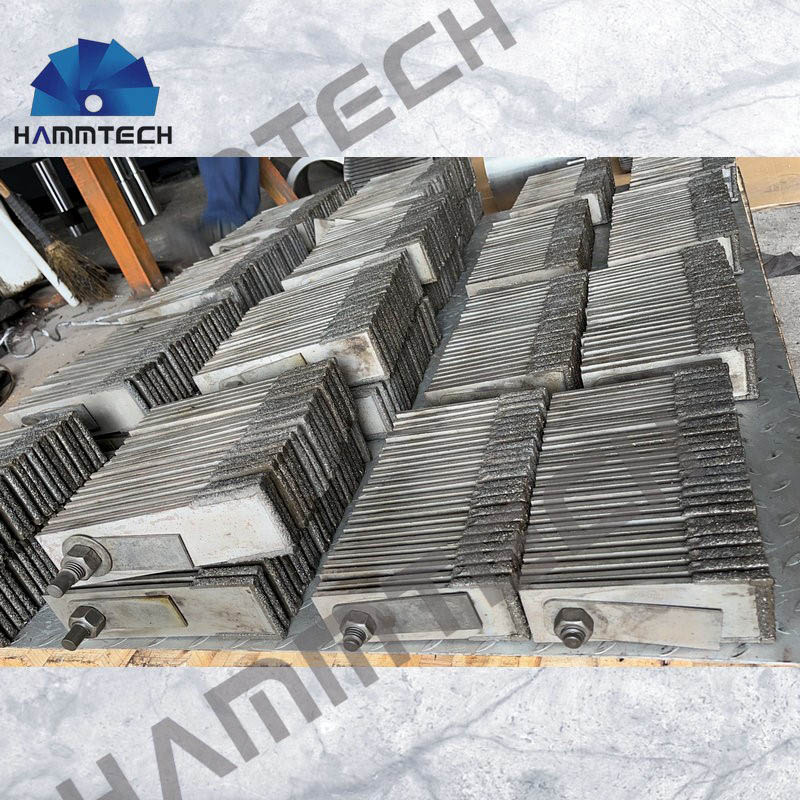
Data de publicación: 28 de febreiro de 2025